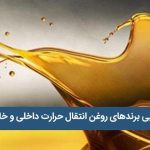
ارزیابی برندهای روغن انتقال حرارت داخلی و خارجی
مارس 1, 2025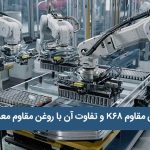
روغن مقاوم K68 و تفاوت آن با روغن مقاوم معمولی
مارس 8, 2025کنترل کیفیت و استفاده بهینه از روغن کمپرسور
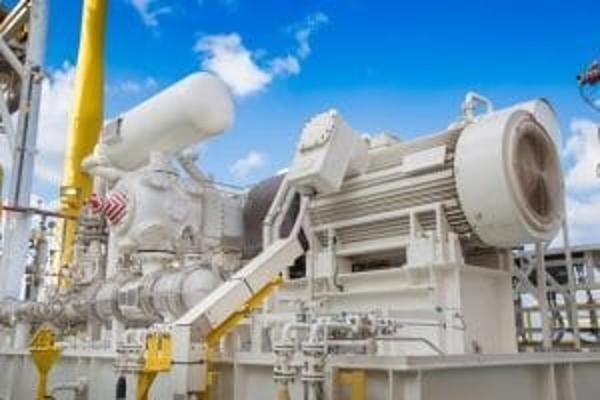
استفاده بهینه روغن کمپرسور
◄راهنمای جامع و تخصصی برای صنایع مختلف►
استفاده بهینه روغن کمپرسور: روغن کمپرسور یکی از اجزای کلیدی در سیستم های فشردهسازی هوا و گاز است که نقش مهمی در کاهش اصطکاک، خنککنندگی و افزایش عمر مفید قطعات کمپرسور دارد. کیفیت روغن کمپرسور تأثیر مستقیمی بر عملکرد دستگاه دارد و در صورت عدم رعایت استاندارد های کیفی، مشکلاتی همچون افزایش سایش، کاهش راندمان و افزایش هزینه های تعمیر و نگهداری رخ می دهد. در این مقاله به سؤالات مهم در این زمینه پرداخته و راهکار هایی برای بهینهسازی عملکرد کمپرسور ها ارائه می دهیم.
در این مقاله با این موضوعات همراه ما باشید.
- اهمیت توجه به کیفیت روغن کمپرسور
- کاربرد روغن کمپرسور
- آزمایش های لازم برای بررسی کیفیت روغن کمپرسور
- علل افزایش ویسکوزیته روغن کمپرسور همراه با ذکر یک تجربه عینی
- راه های جلوگیری از خرابی زودرس روغن کمپرسور
- روش نگهداری بهینه از روغن کمپرسور
- زمان تعویض روغن کمپرسور
اهمیت توجه به کیفیت روغن کمپرسور
کیفیت روغن کمپرسور تأثیر مستقیمی بر عملکرد سیستم های هوای فشرده دارد. روغن های بیکیفیت یا آلوده می توانند مشکلات مختلفی بشرح ذیل ایجاد کنند.
- افزایش سایش قطعات
روغن های نامرغوب نمی توانند به درستی از قطعات متحرک محافظت کنند، که باعث افزایش اصطکاک و استهلاک سریعتر قطعات می شود.
- تشکیل لجن و رسوبات
آلودگی روغن منجر به تشکیل رسوبات کربنی و لجن در روغن کمپرسور شده و بازدهی را کاهش می دهد.
- کاهش راندمان خنککنندگی
روغن های بیکیفیت ممکن است خواص انتقال حرارت مناسبی نداشته باشند که باعث افزایش دمای کاری کمپرسور و کاهش عمر مفید آن می شود.
- افزایش هزینه های تعمیر و نگهداری
روغن های بیکیفیت باعث افزایش دفعات سرویس و تعمیر تجهیزات می شوند که هزینه های عملیاتی را بالا می برد.
- خطرات ایمنی
روغن های آلوده یا بیکیفیت می توانند باعث افزایش خطر آتشسوزی و خرابی سیستم شوند.
تجربه ای از خسارت ناشی از عدم توجه به کنترل کیفیت روغن کمپرسور
یک کارخانه تولید قطعات فلزی از یک کمپرسور اسکرو 160 کیلووات برای تأمین هوای فشرده مورد نیاز خط تولید استفاده می کرد. علی رغم اینکه اپراتور ها به طور منظم فیلتر ها را تعویض می کردند، اما به کیفیت روغن کمپرسور توجه خاصی نداشتند و بدون توجه به وضعیت روغن در حال کار، تنها بر اساس زمانبندی روغن را عوض می کردند.
پس از حدود 3 هزار ساعت کارکرد، کمپرسور دچار افزایش ناگهانی دمای روغن و فشار بیش از حد در مدار روغن شد. در نهایت، کمپرسور به طور ناگهانی خاموش شد و دیگر روشن نشد. بعد از بررسی مشخص شد که روغن کمپرسور به شدت اکسید شده و در مسیر های روغن، رسوبات لجن و کربن تشکیل شده است.
علت اصلی به وجود آمدن این مشکل، افزایش خارج از کنترل عدد اسیدی (TAN) روغن مورد استفاده و ویسکوزیته غلیظتر از حد استاندارد آن تشخیص داده شد، این امر نشان های از اکسیداسیون شدید روغن بود. همچنین سیستم خنککننده به درستی کار نمی کرد و اپراتور ها آن را بررسی نکرده بودند که باعث افزایش سریع دمای روغن شده بود و در نتیجه ذرات ناشی از تجزیه روغن و آلودگی ها در فیلتر و مسیر روغن انباشته شدند و موجب گرفتگی و کاهش جریان روغن گردید.
نکته قابل توجه این بود که آزمایشات دور های روغن (از قبیل انجام تست RPVOT و تست عدد اسیدی) باعث شده بود که خرابی روغن قبل از ایجاد خسارت تشخیص داده نشود و این امر موجب سوختن یاتاقان های اصلی کمپرسور به دلیل عدم روانکاری مناسب گردید.
با توجه به توضیحات فوق، توصیه می گردد حتما موارد زیر در دستور کار قرار بگیرد.
- بررسی دور های کیفیت روغن کمپرسور از طریق تست های ویسکوزیته، عدد اسیدی و میزان آلودگی
- تعویض روغن بر اساس تحلیل آزمایشگاهی، نه فقط زمان کارکرد
- نظارت مداوم بر عملکرد سیستم خنککننده برای جلوگیری از افزایش دما به صورت مستمر
- استفاده از روغن مناسب با استاندارد های توصیه شده
- تعویض روغن پیش از کاهش کیفیت آن
عدم توجه به کیفیت روغن و انجام آزمایش های کنترل کیفی می تواند منجر به خرابی های پرهزینه، توقف تولید و کاهش طول عمر کمپرسور شود. این اتفاق نشان می دهد که کنترل منظم کیفیت روغن کمپرسور یک هزینه اضافی نیست، بلکه یک سرمایهگذاری برای جلوگیری از خسارات سنگین است.
کاربرد روغن کمپرسور
روغن کمپرسور در طیف وسیعی از صنایعی که از هوای فشرده استفاده می کنند، مورد استفاده قرار می گیرد. برخی از مهمترین این صنایع بشرح ذیل می باشد.
- صنایع خودروسازی (رنگکاری، مونتاژ، تست تجهیزات)
- صنایع غذایی و نوشیدنی (بستهبندی و فرآوری مواد غذایی)
- نیروگاه ها (سیستم های ابزاردقیق کنترل تجهیزات و سیستم های خنککننده)
- صنایع الکترونیک (ساخت و مونتاژ قطعات)
- صنایع دارویی و پزشکی (فرآوری دارو ها و ساخت تجهیزات پزشکی)
- کارخانجات سیمان و بتن (تجهیزات مکانیکی و هیدرولیکی)
- صنایع نفت، گاز و پتروشیمی (استفاده در خطوط تولید استخراج و پالایش)
برای مشاوره رایگان و خرید روغن کمپرسور همین الان با 02128424600 تماس بگیرید.
آزمایش های لازم برای بررسی کیفیت روغن کمپرسور
1.ویسکوزیته در دما های مختلف
این آزمایش توسط ویسکومتر کینماتیکی و بر اساس استاندارد ASTM D445 انجام می شود. مقدار ویسکوزیته باید در محدوده مشخصشده توسط سازنده کمپرسور و بر اساس استاندارد ISO VG باشد. در صورت پایین بودن غیر استاندارد ویسکوزیته، روانکاری کاهش یافته و سایش افزایش می یابد؛ در این حالت باید روغن تعویض یا افزودنی های بهبود دهنده ویسکوزیته اضافه شود. در صورت بالا بودن غیر استاندارد ویسکوزیته روغن، جریان روغن مختل شده و دمای عملیاتی افزایش می یابد که نیازمند تعویض روغن می باشد.
2. پایداری اکسیداسیون
در این آزمون زمان اکسیداسیون روغن در شرایطی مشخص اندازه گیری می شود و معمولاً این زمان باید بالای ۱۰۰ دقیقه برای روغن های کمپرسور باشد. اگر زمان پایداری اکسیداسیون پایین باشد، روغن سریعتر تجزیه شده و تشکیل لجن و اسید های مضر زودتر حاصل می شود. در این حالت باید روغن تعویض شده یا از افزودنی های ضد اکسیداسیون استفاده شود.
3. نقطه اشتعال (Flash Point)
این تست، توسط دستگاه اندازه گیری نقطه اشتعال به روش بسته یا باز انجام می شود. نقطه اشتعال باید بالاتر از مقدار تعیینشده توسط سازنده باشد (معمولاً بالای ۲۰۰ درجه سانتیگراد). در صورت کاهش نقطه اشتعال، ممکن است روغن با سوخت یا حلال ها آلوده شده باشد. در این حالت روغن باید تعویض شده و منبع آلودگی بررسی و رفع شود.
4. عدد اسیدی
این آزمایش توسط تیتراسیون با محلول استاندارد پتاسیم هیدروکسید (KOH) طبق استاندارد ASTM D664 انجام می شود. مقدار TAN باید پایین و در محدوده توصیهشده سازنده باشد (معمولاً زیر 0/5mg KOH/g برای روغن های تازه). مقدار بالای TAN نشاندهنده اکسیداسیون شدید و تشکیل اسید است که منجر به خوردگی قطعات می شود. در این حالت باید روغن تعویض شده و فیلتر ها بررسی شوند.
5. مقدار آب و آلودگی
می زان آب توسط تیتراسیون و آلودگی های جامد با روش Patch Test بررسی می شود. مقدار آب باید کمتر از ۰.۰۵٪ (500ppm) باشد و آلودگی های جامد نیز در محدوده مجاز برای کمپرسور باقی بمانند. در صورت وجود آب، باید منبع ورود رطوبت شناسایی شود و با تعویض روغن، استفاده از فیلتر های رطوبتگیر و خشککننده (Dehydration Unit) مشکل برطرف گردد. برای آلودگی های جامد، فیلتر ها باید بررسی و تعویض شوند.
نمونه ای از دیتا شیت کنترل وضعیت آب در نمونه های گرفته شده از روغن
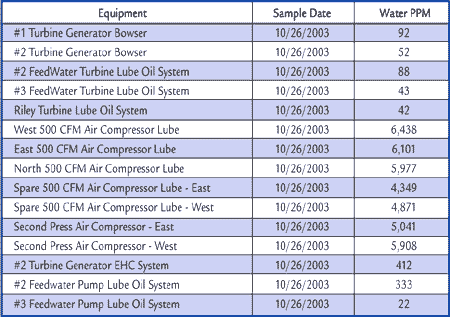
استفاده بهینه روغن کمپرسور
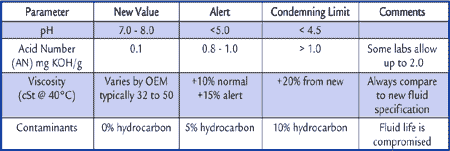
استفاده بهینه روغن کمپرسور
جدول فوق شامل چهار پارامتر کلیدی PH، عدد اسیدی (AN)، ویسکوزیته و میزان آلودگی (Contaminants) برای ارزیابی کیفیت روغن کمپرسور است. این پارامتر ها نقش مهمی در تعیین سلامت روغن و تشخیص زمان تعویض آن دارند.
مقدار نرمال PH (میزان اسیدی یا بازی بودن روغن) 7.0 – 8.0، حد هشدار آن کمتر از 0.5 و حد غیرقابل قبول کمتر از 4.5 می باشد. PH روغن باید در محدوده خنثی (7.0 – 8.0) باشد. اگر این مقدار کاهش یابد، نشاندهنده افزایش اسیدیته روغن است که معمولاً ناشی از اکسیداسیون روغن و تشکیل ترکیبات اسیدی می باشد. در صورتی که PH زیر 0.5 برود، روغن در وضعیت هشدار قرار می گیرد و در PH زیر 4.5 دیگر قابل استفاده نیست و باید تعویض شود.
مقدار نرمال عدد اسیدی 0.1 mg KOH/g، حد هشدار 0.8 – 1.0 mg KOH/g و حد غیرقابل قبول بیشتر از 1.0 mg KOH/g می باشد. عدد اسیدی میزان اسید های تولیدشده در روغن را نشان می دهد. در حالت عادی، عدد اسیدی باید کمتر از 0.1 mg KOH/g باشد. اگر این مقدار به 0.8 – 1.0 mg KOH/g برسد، نشانهی شروع فرآیند اکسیداسیون و تشکیل اسید های مضر است. اگر این مقدار از 1.0 بالاتر برود، یعنی روغن بیش از حد اکسید شده و نیاز به تعویض دارد. برخی آزمایشگاه ها مقدار حداکثر 2.0 mg KOH/g را نیز قابل قبول می دانند.
مقدار نرمال ویسکوزیته، بسته به توصیهی OEM معمولاً 32 تا 50CST بوده حد هشدار +10% (وضعیت نرمال) +15% (وضعیت هشدار) و حد غیرقابل قبول، افزایش بیش از +20% از مقدار اولیه می باشد. ویسکوزیته نقش اساسی در عملکرد روغن کمپرسور دارد. اگر ویسکوزیته بیش از 10 تا 15 درصد افزایش یابد، باید بررسی شود. اگر بیش از 20% افزایش یابد، روغن دیگر مناسب نیست و باید تعویض شود. این افزایش معمولاً به دلیل آلودگی، تجزیه مولکولی روغن یا اکسیداسیون رخ می دهد.
مقدار نرمال آلودگی 0% هیدروکربن، حد هشدار 5% هیدروکربن و حد غیرقابل قبول 10% هیدروکربن می باشد. وجود آلودگی های هیدروکربنی در روغن، نشاندهندهی ورود آلودگی خارجی به سیستم یا تخریب روغن در اثر دمای بالا و اکسیداسیون شدید است. اگر میزان آلودگی از 5% عبور کند، باید وضعیت روغن تحت نظر باشد و اگر از 10% بالاتر رود، روغن دیگر قابل استفاده نیست و سیستم نیز ممکن است دچار گرفتگی شود.
این جدول نشان می دهد که کنترل دقیق پارامتر های روغن کمپرسور ضروری است. مهمترین اقدامات شامل کنترل عدد اسیدی (AN) و pH برای جلوگیری از اکسیداسیون و تخریب روغن، مقایسه مداوم ویسکوزیته روغن با مقدار اولیه و عدم اجازهی افزایش بیش از 15 تا 20 درصد، بررسی میزان آلودگی و جلوگیری از ورود ذرات خارجی و هیدروکربن ها و تعویض روغن در زمان مناسب بر اساس آنالیز آزمایشگاهی، نه صرفاً بر اساس زمان کارکرد، می باشد.
پیشنهاد می گردد برای حفظ کیفیت روغن کمپرسور و افزایش عمر مفید دستگاه، آزمایش های کنترل کیفیت را به صورت دوره ای انجام دهید و در صورت مشاهده تغییرات غیرعادی، اقدام به تعویض روغن یا بررسی عملکرد سیستم نمایید.
علل افزایش ویسکوزیته روغن کمپرسور
- آلودگی روغن به مواد خارجی (گرد و غبار، رسوبات یا مواد افزودنی نامناسب)
حتی اگر فیلتر نو باشد، ممکن است آلودگی های باقیمانده در سیستم، مثلاً ذراتی که در هنگام تعمیر در مدار مانده اند، باعث تغییر در خواص روغن گردد.
- افزایش دمای بیش از حد در بخش هایی از سیستم
ممکن است در برخی نقاط کمپرسور، به ویژه در مسیر جریان روغن، دمای بالا باعث تبخیر اجزای سبکتر روغن و افزایش ویسکوزیته آن شود. این موضوع معمولاً در کمپرسور هایی که دچار مشکلات خنککاری هستند، دیده می شود.
- مخلوط شدن روغن جدید با باقیمانده روغن قدیمی نامناسب
اگر روغن قدیمی با نوع متفاوتی از روغن جدید مخلوط شده باشد، امکان دارد ناسازگاری شیمیایی باعث تغییر خواص آن شود.
- اکسیداسیون روغن در اثر کارکرد تحت فشار یا وجود آلودگی های کاتالیزوری
گاهی ذراتی از فلزاتی مانند مس و آهن که از قطعات داخلی سیستم جدا شده و وارد روغن شده اند، می توانند به عنوان کاتالیزور، واکنش های اکسیداسیونی را تسریع کنند و باعث افزایش ویسکوزیته شوند.
- مشکل در سیستم تهویه یا برگشت روغن
اگر برگشت روغن به درستی انجام نشود یا گاز های حاوی بخار روغن در سیستم تهویه به درستی جدا نشوند، روغن ممکن است غلیظتر شود.
با توجه به توضیحات فوق، موارد ذیل توصیه می گردد.
- با انجام تست های بیشتر روی روغن در حال کار، ازجمله بررسی عدد اسیدی (TAN)، عدد اکسیداسیون و بررسی وجود فلزات و آلودگی های احتمالی، منبع مشکل را شناسایی کنید.
- از دماسنج های لیزری یا حسگر های دمایی برای بررسی نقاطی که احتمال افزایش دمای غیرعادی دارند، استفاده نمایید.
- سیستم را به طور کامل از روغن قدیمی تخلیه و شستشو دهید.
- از اصل بودن و مناسب بودن فیلتر روغن اطمینان حاصل کنید. زیرا اگر آلودگی یا هوای اضافی وارد سیستم شود، می تواند باعث تغییرات نامطلوب در روغن شود.
- وضعیت اتصالات و شیر های سیستم را به صورت دقیق بررسی نمایید.
تجربه عینی:
در یک مورد تجربه عینی در یک کارخانه، با وجود اطمینان از سلامت کمپرسور، نو بودن فیلتر ها و کیفیت روغن، کارشناسان واحد تعمیر و نگهداری شاهد افزایش ویسکوزیته روغن کمپرسور از 68 به 85 بعد از 1000 ساعت کارکرد کمپرسور بودند که این امر نشاندهنده یک مشکل در عملکرد سیستم بود و پس از بررسی موضوع با جایگزین نمودن روغن 68 با روغن مناسب برای سیستم با ویسکوزیته 57، مشکل به صورت کلی برطرف گردید. در این مورد دلایل این امر را بشرح ذیل می توان بیان نمود.
- غلظت
اگر سیستم کمپرسور به هر دلیلی نتواند ویسکوزیته 68 را به درستی پمپاژ و روانکاری کند، ممکن است فشار در مسیر های روغن بالا رود و باعث افزایش دمای موضعی و در نهایت تغییر خواص روغن شود. استفاده از روغن با ویسکوزیته کمتر و برابر 57 باعث شده روغن راحتتر در مدار جریان پیدا کند و از ایجاد نقاط داغ (Hot Spot) جلوگیری شود.
- آلودگی روغن قبلی
احتمالا روغن 68 که قبلاً استفاده شده، دارای ناخالصی یا نوعی ناسازگاری با سیستم بوده است. این می تواند باعث اکسیداسیون سریعتر و افزایش ویسکوزیته شود. روغن ویسکوزیته 57 فرمولاسیون متفاوتی داشته و در برابر شرایط کاری کمپرسور بهتر عمل کرده است.
- سیستم خنککننده
اگر روغن 68 در دما های بالاتر از حد طبیعی کار می کرد، ممکن بود برخی ترکیبات سبک آن تبخیر شوند و باعث غلیظ شدن روغن باقیمانده شود. روغن 57 با گرانروی کمتر، می تواند به کاهش دما کمک کرده و مانع از پدیده تخریب زودرس شود.
- انتخاب بر اساس شرایط واقعی کارکرد کمپرسور
ویسکوزیته پیشنهادی توسط سازنده ممکن است بر اساس شرایط ایده آل باشد، اما در شرایط واقعی (مثل دمای محیط، فشار کمپرسور، طراحی سیستم) ویسکوزیته 57 عملکرد بهتری داشته است. بنابراین، در برخی موارد انتخاب روغن با ویسکوزیته کمتر (در محدوده مجاز) می تواند به بهبود عملکرد کمک کند.
درنتیجه استفاده از روغن با ویسکوزیته 68 برای شرایط کاری کمپرسور مذکور مناسب نبوده یا ترکیب شیمیایی آن مشکل داشته است و استفاده از روغن 57 باعث کاهش مقاومت در برابر جریان، بهبود خنککاری و جلوگیری از افزایش غیرعادی ویسکوزیته شده است. لذا در چنین شرایطی تست دوره ای برای بررسی وضعیت کمپرسور پس از چند صد ساعت کارکرد ضروری است تا مطمئن شوید که همچنان کیفیت روغن کمپرسور در محدوده استاندارد باقی می ماند.
راه های جلوگیری از خرابی زودرس روغن کمپرسور
عوامل مختلفی می توانند باعث تخریب زودرس روغن شوند که نتیجه آن کاهش کارایی کمپرسور، افزایش هزینه های نگهداری و حتی آسیب جدی به تجهیزات خواهد بود. برای جلوگیری از خرابی زود هنگام روغن کمپرسور مواردی به شرح زیر توصیه می گردد.
1.کنترل دمای کاری کمپرسور
افزایش بیش از حد دما می تواند باعث اکسیداسیون سریع روغن، تجزیه مولکولی و تشکیل لجن و کربن در سیستم شود. این موضوع باعث کاهش خاصیت روانکاری، گرفتگی فیلتر ها و افزایش سایش قطعات می شود.
از عملکرد صحیح سیستم خنککننده اطمینان حاصل کرده و رادیاتور ها و مبدل های حرارتی را تمیز نگه دارید. سطح و کیفیت روغن به طور منظم بررسی، از روغن هایی با پایداری حرارتی بالا که برای دما های عملیاتی کمپرسور مناسب باشند، استفاده کنید. حسگر های دمایی نصب نموده و سیستم قطع اضطراری در صورت افزایش بیش از حد دما تنظیم نمایید.
2. انتخاب روغن مناسب بر اساس شرایط عملیاتی
هر کمپرسور بسته به نوع، فشار کاری، دمای عملیاتی و محیط کار نیاز به روغن خاصی دارد. استفاده از روغن نامناسب می تواند منجر به تشکیل لجن، افزایش اصطکاک و کاهش راندمان کمپرسور شود.
لذا به توصیه های سازنده کمپرسور برای انتخاب گرید ویسکوزیته و نوع روغن توجه نموده و از روغن های سنتتیک برای دما های بالا یا شرایط سخت عملیاتی که طول عمر بیشتری دارند، استفاده نمایید. همچنین از سازگاری روغن جدید با روغن قبلی در صورت تغییر نوع روغن مطمئن شده و شاخص پایداری حرارتی و اکسیداسیون روغن قبل از خرید را بررسی نمایید.
3. تعویض منظم فیلتر های روغن
فیلتر های روغن وظیفه حذف ذرات معلق، آلاینده ها و محصولات تجزیه روغن را بر عهده دارند. اگر فیلتر ها اشباع شوند، آلودگی ها به داخل کمپرسور راه پیدا کرده و باعث سایش و کاهش عملکرد روغن خواهند شد.
استفاده از فیلتر های باکیفیت با درجه فیلتراسیون مناسب برای کمپرسور، بررسی دوره ای وضعیت فیلتر و تعویض آن طبق برنامه نگهداری پیشگیرانه و در صورت وجود افزایش افت فشار در فیلتر ها، بررسی سیستم و جایگزینی فیلتر های مسدود، از اقدامات مهم در این خصوص می باشد.
4. جلوگیری از ورود آب و ذرات خارجی به روغن
آب و آلاینده های خارجی می توانند باعث افزایش خوردگی، کاهش خاصیت روانکاری، و تجزیه زودرس روغن شوند. وجود رطوبت بالا همچنین می تواند باعث تشکیل امولسیون و انسداد مسیر های روغن شود.
نصب سیستم های رطوبتگیر در کمپرسور برای کاهش ورود آب به روغن، استفاده از آزمایش کارل فیشر به صورت دوره ای برای اندازهگیری میزان آب در روغن، نگهداری مخازن ذخیره روغن در محیط خشک و جلوگیری از آلودگی در هنگام تعویض روغن و استفاده از فیلتر های جداساز رطوبت برای جلوگیری از ورود آب به سیستم، می بایست انجام گیرد.
با توجه به توضیحات فوق، با کنترل دمای عملیاتی، انتخاب روغن مناسب، تعویض منظم فیلتر ها و جلوگیری از ورود آلاینده ها، می توان عمر مفید روغن کمپرسور را به میزان قابلتوجهی افزایش داد. این اقدامات نه تنها باعث کاهش هزینه های تعمیر و نگهداری خواهند شد، بلکه بهرهوری و طول عمر کمپرسور را نیز افزایش می دهند. پیادهسازی یک برنامه نگهداری منظم و انجام آزمایش های دوره ای می تواند از خرابی زودرس روغن و مشکلات ناشی از آن جلوگیری کند.
برای تهیه روغن های اختصاصی مطابق با نیاز کمپرسور های خود و شرایط عملیاتی خاص از طریق فرم تولید روغن کمپرسور سفارشی اقدام کنید.
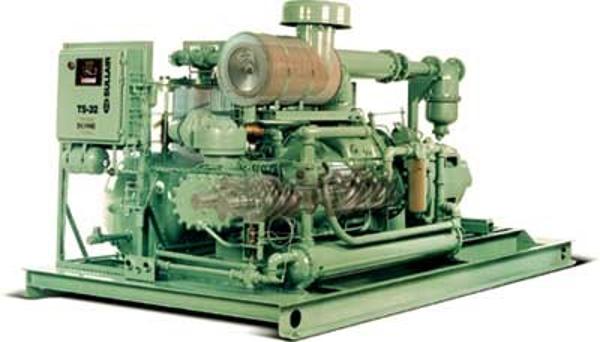
استفاده بهینه روغن کمپرسور
روش نگهداری بهینه از روغن کمپرسور
نگهداری صحیح از روغن کمپرسور نقش کلیدی در افزایش عمر مفید آن، بهبود عملکرد کمپرسور و کاهش هزینه های نگهداری دارد. روغن کمپرسور تحت تأثیر عوامل محیطی مانند رطوبت، آلودگی و اکسیداسیون قرار می گیرد، بنابراین رعایت اصول صحیح ذخیرهسازی و نگهداری می تواند از خرابی زودرس روغن و آسیب به دستگاه جلوگیری کند. در ادامه، مهمترین روش های بهینه نگهداری روغن کمپرسور بررسی می شود.
- نگهداری روغن در ظروف آب بند و محیطی مناسب
قرار گرفتن روغن در معرض رطوبت، گرد و غبار و سایر آلودگی های محیطی می تواند باعث کاهش کیفیت آن و ایجاد مشکلاتی مانند افزایش ویسکوزیته، تشکیل لجن و کاهش خاصیت روانکاری شود.
استفاده از ظروف دربسته و با آب بندی کامل برای جلوگیری از ورود گرد و غبار، رطوبت و آلودگی های خارجی، نگهداری ظروف روغن در محیط خشک و خنک، دور از تابش مستقیم نور خورشید و منابع حرارتی، عدم نگهداری روغن در مجاورت مواد شیمیایی خورنده که می توانند روی ترکیبات روغن تأثیر بگذارند و برچسبگذاری مناسب ظروف روغن برای جلوگیری از اشتباه در انتخاب و استفاده از روغن، ضروری می باشد.
- بررسی دوره ای کیفیت روغن
با گذشت زمان، روغن کمپرسور تحت تأثیر شرایط عملیاتی و محیطی تغییر می کند. انجام آزمایش های دوره ای کمک می کند تا مشکلات احتمالی قبل از تأثیرگذاری بر عملکرد کمپرسور شناسایی و برطرف شوند. مهمترین تست ها و آزمایشات مربوطه بشرح ذیل می باشد.
- انجام آزمایش ویسکوزیته در دما های مختلف برای بررسی تغییرات خواص روانکاری
- اندازهگیری عدد اسیدی (TAN) جهت ارزیابی میزان اسید های تشکیلشده در روغن
- انجام آزمایش RPVOT برای بررسی مقاومت روغن در برابر اکسیداسیون
- استفاده از تست کارل فیشر برای اندازهگیری میزان آب موجود در روغن
- تحلیل نتایج آزمایشات و تعویض به موقع روغن در صورت مشاهده افت کیفیت آن، از موضوعاتی است که توسط کارشناسان واحد تعمیر و نگهداری باید به صورت مستمر پیگیری شود.
- جلوگیری از تماس روغن با هوا و رطوبت
اکسیژن موجود در هوا می تواند باعث اکسیداسیون روغن شده و در نتیجه منجر به تولید ترکیبات اسیدی، افزایش ویسکوزیته و کاهش خاصیت روانکاری شود. همچنین، رطوبت می تواند باعث تشکیل امولسیون و افزایش احتمال خوردگی قطعات شود.
بستن کامل درب ظروف روغن پس از هر بار استفاده، استفاده از نیتروژن برای پر کردن فضای خالی مخازن روغن در صورت امکان، برای کاهش تماس با اکسیژن، جلوگیری از ورود آب و رطوبت به سیستم با استفاده از فیلتر های جداساز آب و نگهداری ظروف روغن در ارتفاع مناسب از سطح زمین برای کاهش احتمال جذب رطوبت، به این امر کمک می کند.
با رعایت اصول نگهداری از روغن کمپرسور، از جمله نگهداری در ظروف دربسته، انجام آزمایش های دوره ای و جلوگیری از تماس با هوا و رطوبت، می توان از افت کیفیت روغن و مشکلات عملیاتی کمپرسور جلوگیری کرد. پیادهسازی یک برنامه منظم برای نظارت بر وضعیت روغن و شرایط ذخیرهسازی، علاوه بر افزایش عمر مفید روغن، باعث کاهش هزینه های تعمیر و نگهداری کمپرسور نیز خواهد شد.
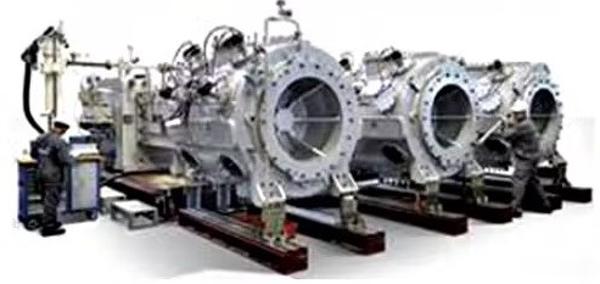
استفاده بهینه روغن کمپرسور
برای مشاوره رایگان و خرید روغن کمپرسور همین الان با 02128424600 تماس بگیرید.
زمان تعویض روغن کمپرسور
با گذشت زمان و تحت تأثیر شرایط عملیاتی، روغن کمپرسور به تدریج کیفیت خود را از دست داده و نیاز به تعویض پیدا می کند. تشخیص به موقع زمان تعویض روغن می تواند از آسیب های جدی به قطعات کمپرسور جلوگیری کند و هزینه های تعمیر و نگهداری را کاهش دهد. در ادامه، مهمترین نشانه های زمان تعویض روغن بررسی می شود.
- افزایش عدد اسیدی
با گذشت زمان و تحت تأثیر اکسیداسیون، ترکیبات اسیدی در روغن افزایش می یابد. این اسید ها می توانند باعث خوردگی قطعات داخلی کمپرسور شوند. افزایش غیرمعمول عدد اسیدی نشاندهنده تخریب شیمیایی روغن است و نیاز به تعویض آن دارد.
- تغییر رنگ و بوی روغن
روغن کمپرسور در شرایط عادی باید شفاف و بدون بوی نامطبوع باشد. تغییر رنگ به سمت قهوه ای یا سیاه و ایجاد بوی سوختگی نشاندهنده تخریب حرارتی روغن است، که این موضوع موجب افزایش دمای کاری کمپرسور، آلودگی با ذرات فلزی و ترکیبات اکسیدشده و تجزیه ترکیبات شیمیایی روغن در اثر کارکرد طولانی می گردد.
- افزایش ویسکوزیته
ویسکوزیته روغن بر عملکرد روانکاری و کاهش اصطکاک قطعات تأثیر مستقیم دارد. اگر ویسکوزیته افزایش یابد، گردش روغن در سیستم کاهش یافته و فشار بر کمپرسور بیشتر می شود. این موضوع سبب اکسیداسیون و تشکیل ترکیبات پلیمری، آلودگی با گرد و غبار، آب یا مواد خارجی و تبخیر ترکیبات سبک روغن در دما های بالا می گردد. لذا انجام آزمایش ویسکوزیته در دما های مختلف برای بررسی تغییرات نسبت به مقدار استاندارد ضروری می باشد.
- کاهش راندمان سیستم و عملکرد نادرست کمپرسور
روغن نامناسب یا تخریبشده باعث افزایش اصطکاک، کاهش قابلیت خنککنندگی روغن و کاهش بازده کمپرسور می شود. نشانه های این امر افزایش دما و فشار عملیاتی کمپرسور، افزایش مصرف انرژی بدون افزایش خروجی و تولید صدای غیرمعمول به دلیل کاهش خاصیت روانکاری روغن می باشد. در صورت مشاهده این علائم، باید کیفیت روغن بررسی شده و در صورت لزوم تعویض گردد.
جمعبندی و نتیجه گیری
تعویض به موقع روغن کمپرسور تأثیر مستقیمی بر عملکرد و عمر مفید دستگاه دارد. افزایش عدد اسیدی، تغییر رنگ و بو، افزایش ویسکوزیته و کاهش راندمان کمپرسور از نشانه های اصلی نیاز به تعویض روغن هستند. انجام آزمایش های دوره ای بر روی روغن می تواند کمک کند تا زمان تعویض روغن به موقع تشخیص داده شود و از آسیب های جدی به کمپرسور جلوگیری گردد. کیفیت این روغن نه تنها بر طول عمر دستگاه تأثیر می گذارد، بلکه بهرهوری و هزینه های عملیاتی را نیز تحتالشعاع قرار می دهد.
اگر به دنبال عملکرد بهینه و دوام بالاتر کمپرسور خود هستید، با کارشناسان شرکت بازرگانی رجال مشورت کنید و از محصولات استاندارد و باکیفیت بهره ببرید. با تکیه بر دانش فنی و تجربه گسترده، ما آماده ایم تا بهترین راهکار های تخصصی را در زمینه انتخاب، پشتیبانی و استفاده از روغن های صنعتی و کمپرسور ارائه دهیم. اگر به دنبال روغنی هستید که کاملاً با شرایط عملیاتی و نیاز های دستگاه های شما سازگار باشد، می توانید از طریق فرم تولید روغن صنعتی کمپرسور سفارشی، محصولی متناسب با نیاز خود تهیه کنید. کارشناسان ما آماده اند تا شما را در انتخاب، نگهداری و استفاده بهینه از روغن های کمپرسور راهنمایی کنند. برای دریافت مشاوره تخصصی با ما تماس بگیرید 📞 021-28424600
تهیه و تدوین: واحد فنی شرکت بازرگانی رجال صنعت نهاد گستر
برای سفارش روغن های خاص جهت دستگاه های مورد نظر شما میتوانید از سایت رجال از قسمت فرم تولید محصولات سفارشی اقدام کنید.