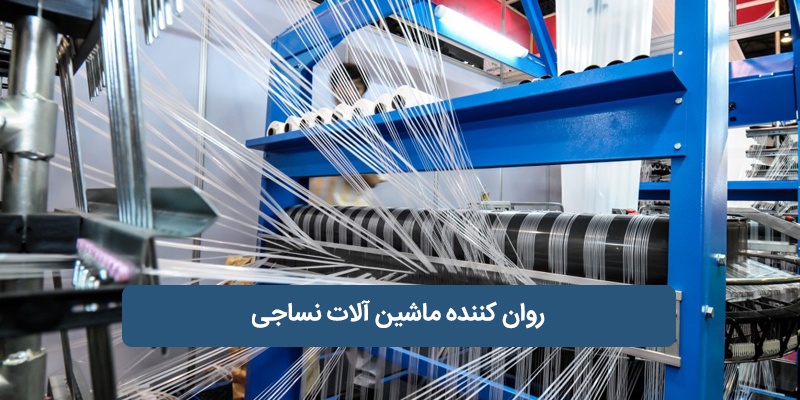
بهترین روان کننده برای ماشین آلات نساجی
اکتبر 1, 2023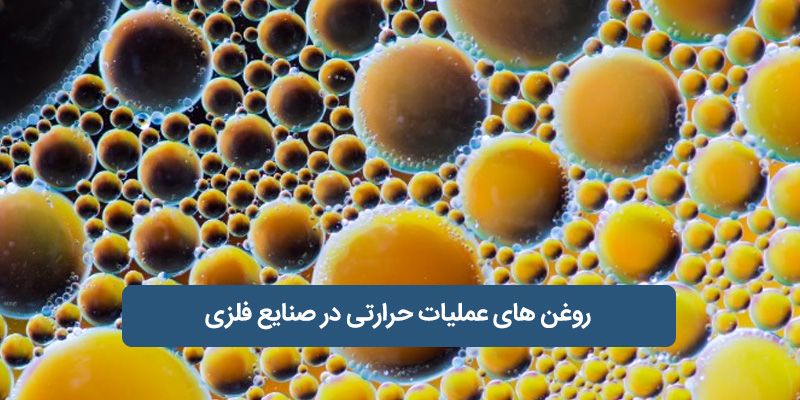
بررسی تشکیل کف و انتشار هوا در روغن دنده صنعتی
فوریه 11, 2024قابلیت های روغن مخصوص عملیات فلز کاری: یکی از سئوالاتی که به کرات از سوی مشتریان شرکت بازرگانی رجال در مورد روغن های عملیات فلزی، مطرح می گردد، سئوال در مورد قابلیت های است که لازم است این روغن ها از آن برخوردار باشند در ادامه، به اختصار، پاسخ به این سئوال داده شده است.

قابلیت های روغن مخصوص عملیات فلز کاری
با توجه به اینکه در حال حاضر، در بازار ایران، روغن های عملیات فلز کاری ایرانی و خارجی و با برند های مختلفی وجود دارند، توصیه می نماییم، در زمان انتخاب و خرید این نوع از روغنها، داشتن قابلیت های به شرح زیر، مد نظر قرار داشته باشد تا در زمان مصرف این نوع از روغنها، کمترین مشکل برای مصرف کنند گان حاصل گردد و این قابلیت ها عبارتند از:
- تشکیل کف به صورت کنترل شده و در کمترین مقدار ممکن، با به کارگیری مواد افزودنی ضد کف قوی در فرمولاسیون ساخت این نوع از روغنها تا کف بیش از حد تشکیل نگردد.
- خاصیت ضد خورد کی قوی، با به کارگیری مواد افزودنی ضد خورندگی قوی، به صورتیکه حداقل خورندگی و زنگ زدگی بر روی سطوح فلزی در تماس به وجود آید.
- کمترین میزان تبخیر تا میزان هدر رفت روغن عملیات فلز کاری در حین استفاده به حداقل رسانده شده و استفاده از این روغنها مقرون به صرفه باشد.
- حداکثر سازگاری با بدن انسان، به صورتیکه در زمان تماس با پوست بدن و یا استنشاق بخارات این روغنها، کمترین میزان تهدید سلامت کارکنان را در بر داشته باشد.
- حداکثر سازگاری با محیط زیست، به نحوی که در زمان دور ریختن این روغنها، اثرات مخرب آنها بر روی محیط زیست، به کمترین حد ممکن کاهش یافته باشد.
- پایداری بالا، هم در زمان مصرف و در شرایط عملیاتی و هم در زمان نگهداری در انبار و قبل از مصرف آنها تا استفاده از این روغن ها مقرون به صرفه تر باشد.
- بالا بودن نقطه اشتعال این روغنها تا احتمال آتش گرفتن و خطرات ناشی از اشتعال آنها، به حداقل ممکن رسانیده شده باشد.
- قابلیت انحلال سریع در آب و تشکیل امولسیون پایدار، برای آن دسته از روغنهای عملیات فلز کاری که در زمان مصرف باید ابتدا با آب مخلوط شده و سپس استفاده گردند.
- دارا بودن مواد ضد رشد باکتری و ضد میکروارگانیسم ها، به اندازه کافی، به نحوی که این روغنها، بالاترین مقاومت را در مقابل رشد باکتریها و میکروارگانیسم ها داشته و دیرتر بو گرفته و در نتیجه فعالیت باکتریها و میکروارگانیسم ها، تخریب شوند.
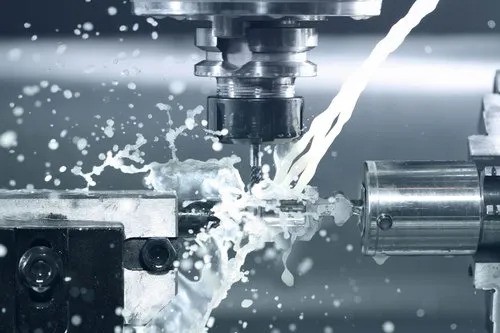
قابلیت های روغن مخصوص عملیات فلز کاری
در خصوص استانداردهای مطرح در مباحث مربوط به روغن صنعتی عملیات فلز کاری (CUTTING OIL) بوده که در ادامه، به اختصار توضیحاتی در این خصوص ارائه شده است.
به صورت کلی، میتوان گفت که استانداردها در مدیریت امور فنی صنایع مختلف، نقش بسیار مهمی را ایفا مینمایند و کیفیت محصولات و انجام درست برنامه های تعمیر و نگهداری تجهیزات خطوط تولید، به رعایت دقیق استانداردهای مربوطه بستگی دارد، در همین رابطه، به دلیل حساسیتهای مربوط به استفاده از روغنهای صنعتی و منجمله روغن فلز کاری (CUTTING OIL) برای این دسته از روغنها نیز استانداردهای خاصی تدوین شده است.
استاندارد اروپایی DIN از جمله استانداردهای بین المللی مورد استفاده در صنایع فلزی کشور ما و بسیاری از کشورهای پیشرفته دیگر دنیا ست و در واقع این دسته از صنایع، مصرف کننده اصلی روغنهای عملیات فلز کاری میباشند، لذا در ادامه، در معرفی این استاندارد، توضیحات بیشتری ارائه خواهیم نمود.
یکی از معتبر ترین موسسات تدوین و تنظیم استانداردها در آلمان، موسسه ملی استاندارد آلمان (Deutsches Institut für Normung) میباشد که به اختصار به DIN معروف است و سالها ست وظیفه تدوین و انتشار استانداردهای فنی در آلمان را بر عهده دارد و استانداردهای رسمی منتشر شده از سوی این موسسه در کاهش قیمت ها، افزایش ایمنی، بهبود کیفیت محصولات و توسعه کمی و کیفی صنایع مختلف، نقش بسیار مهمی را داشته و دارد.

قابلیت های روغن مخصوص عملیات فلز کاری
این موسسه در سال ۱۹۱۷ با عنوان Normenausschuß der deutschen Industrie تاسیس و در ابتدا، نخستین استانداردهای خود را با پیشوند NADI ارائه مینمود اما پس از گذشت چند سال و با گسترش فعالیت های این مجموعه و تدوین استانداردهای بیشتر، در سال ۱۹۲۶ عنوان این مجموعه به نام Deutscher Normenausschuß تغییر داده شد و سپس در سال ۱۹۷۵ با شناخته شدن این موسسه، به عنوان تدوین کننده رسمی استانداردهای ملی آلمان، عنوان موسسه مذکور مجددا به Deutsches Institut für Normung تغییر یافت و از آن پس، استانداردهای این موسسه با پیشوندDIN شناخته شدند. امروزه در سراسر دنیا، استانداردهای این موسسه قدیمی مورد توجه هستند و کارشناسان این موسسه تا کنون با تدوین بیش از ۳۰۰۰۰ عنوان استاندارد، تقریباً برای تمامی علوم و تکنولوژی ها، استاندارد تعریف و تدوین نموده اند.
لازم به ذکر است، استانداردهای DIN آلمان جزو استانداردهای سخت گیرانه مطرح در جهان هستند و اکثر تولید کنند گان بزرگ و معتبر دنیا از این استاندارد برای مدیریت امور فنی مربوط به محصولات خود استفاده مینمایند و لازم به ذکر است که در مباحث مربوط به روغن های عملیات فلز کاری استاندارد DIN 51385 این موسسه یکی از استاندارد های قوی و مطرح در سطح جهانی میباشد.
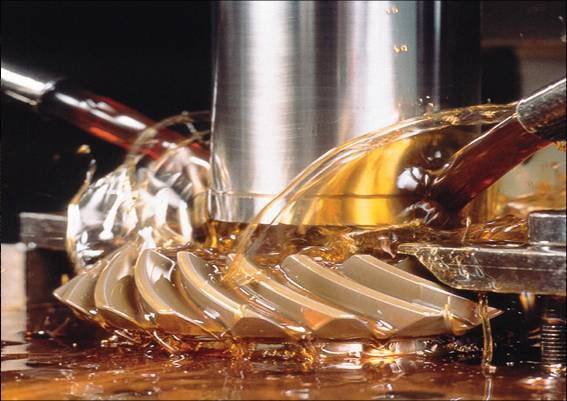
قابلیت های روغن مخصوص عملیات فلز کاری
در استاندارد DIN 51385، بر اساس نحوی استفاده از روغن های عملیات فلز کاری 3 دسته روغن تعریف شده است که عبارتند از:
- روغن عملیات فلز کاری خالص که این نوع از روغن به همان صورت خالص، بسته بندی و مصرف میشود.
- روغن عملیات فلز کاری محلول در آب که در زمان مصرف، ابتدا لازم است، به این دسته از روغنها، آب صنعتی (با مشخصات کنترل شده) اضافه گردد و سپس محلول آبی ساخته شده، به عنوان سیال عملیات فلز کاری، استفاده میشود.
- روغن مخصوص عملیات فلز کاری به صورت امولسیون از روغن که این امولسیون آماده مصرف، در ظروف مخصوص، بسته بندی شده و به محل مصرف ارسال میگردند تا به همان صورت در خطوط مصرف شوند.
انتخاب روغن مناسب از بین انواع روغن های معرفی شده در بالا، از اهمیت بسیار زیادی برخوردار است و جهت انتخاب روغن مناسب، لازم است با کارشناسان شرکت سازنده خطوط تولید و یا سازندگان تجهیزات، مشورت نمود و در صورتیکه این کارشناسان در دسترس نباشند، میتوان تحقیق نمود در خطوط تولید مشابه با تجهیزات مشابه از چه نوع روغنی استفاده میشود و یا با کارشناسان شرکتهای معتبر تامین کننده روغنهای صنعتی مشورت نمود.
خاطر نشان می سازیم، در صورت وجود سوالات بیشتری در مورد روغن های صنعتی و منجمله سیا لات و روغنهای مخصوص عملیات فلز کاری (CUTTING OIL)، کارشناسان واحد فروش شرکت بازرگانی رجال جهت ارائه مشاوره های فنی و تخصصی، همواره در خدمت مشتریان گرامی می باشند.
در هنگام استفاده از روغن های عملیات فلزکاری با چه مشکلاتی روبرو خواهیم بود؟
استفاده از روغن های عملیات فلزکاری در صنایع مختلف، همراه است با بروز برخی مشکلات که در ادامه به این موارد و راه حل های پیشنهادی جهت حل نمودن این مشکلات می پردازیم ولی قبل از آن لازم است به این نکته اشاره گردد که روغنهای عملیات فلزکاری دو دسته هستند و عبارتند از:
- روغن عملیات فلزکاری که بصورت خالص استفاده میگردد (Neat cutting fluid)
- روغن عملیات فلزکاری که از نوع روغن های حل شونده در آب (Soluble oil) هست و بصورت امولسیون شیری رنگ روغن در آب استفاده میگردد (water _ miscible cutting fluid)

قابلیت های روغن مخصوص عملیات فلز کاری
موارد مربوط به استفاده از روغنهای عملیات فلزکاری که بصورت خالص استفاده میگردند به شرح ذیل میباشد:
- مشکل گرفتگی فیلترها: در صورتیکه ویسکوزیته روغن بیش از حد زیاد گردد شدت جریان عبور روغن از فیلتر کاهش یافته و در نتیجه عملکرد فیلتر با مشکل مواجه میگردد که در این رابطه میتوان با اضافه کردن روغن تازه و یا جداسازی مستمر توده هایی چسبنده شناور در روغن (نظیر صمغ ها که باعث تسریع در گرفتگی فیلتر روغن شده اند) این مشکل را حل نمود.
- کاهش عمر مفید قطعات: با افزایش میزان آلودگی روغن، عمر مفید قطعات در تماس با روغن عملیات فلزکاری کاهش میابد و این آلودگی میتواند ناشی از ورود ذرات گرد و غبار یا آب یا گریس و یا روغنهای صنعتی دیگری باشد که به تدریج به داخل روغن عملیات فلزکاری نشت کرده اند و با افزایش تعداد فیلترها و استفاده از مکانیزم های فیلتراسیون پیشرفته تر میتوان با سرعت و راندمان بالاتری آلودگی ها را از روغن عملیات فلزکاری خارج نمود، همچنین میتوان با انجام برخی آزمایش ها در صورتیکه مقادیر برخی از مواد افزودنی روغن عملیات فلزکاری کاهش یافته باشد با نظر کارشناسان کنترل کیفی روغن، به مقدار لازم مواد افزودنی از دست رفته را اضافه نموده و کمبود ها را جبران کرد.
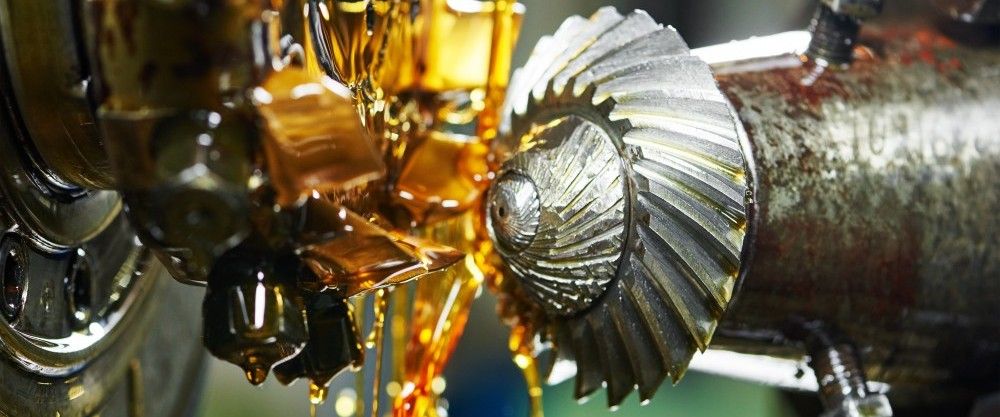
قابلیت های روغن مخصوص عملیات فلز کاری
تشکیل کف: در صورتیکه در روغن عملیات فلزکاری در حین کار کف مشاهده کردد این کف میتواند ناشی از مواردی به شرح زیر باشد:
- ورود آب یا رطوبت به روغن که در این حالت لازم است در اسرع وقت و با مشاهده کف، محل نشت آب یا رطوبت پیدا شده و از ورود آب به درون روغن جلوگیری بعمل آورده شود.
- ورود روغن های سرگردان دیگر یا گریس ها به روغن که در این حالت لازم است با مشاهده کف، در اسرع وقت، محل نشت روغن های سرگردان یا گریسهای نشت پیدا کرده پیدا شده و از ورود آنها به درون روغن جلوگیری بعمل آورده شود همچنین میتوان برای کنترل کف، مواد افزودنی ضد کف را به اندازه لازم به محفظه روغن اضافه نمود.
- افزایش بیش از حد دمای روغن که در این صورت میتوان، با استفاده از یک سیستم سرد کننده مناسب، بصورت مستمر، دمای روغن عملیات فلزکاری در حال کار را کنترل نمود.
- افزایش بیش از حد سرعت جریان سیرکولاسیون روغن: در صورتیکه سرعت سیرکولاسیون روغن در محفظه روغن عملیات فلزکاری بیش از حد گردد این میتواند منجر به تشدید تشکیل کف شده و لذا لازم است در این حالت سرعت جریان سیرکولاسیون روغن را تنظبم مجدد نمود.
- تشکیل کف ممکن است ناشی از انتخاب نادرست نوع روغن عملیات فلزکاری متناسب با سیستم فیلتراسیون و سیستم سیرکولاسیون باشد که در این صورت باید با مشورت شرکت سازنده تجهیزات عملیات فلزکاری، نوع مناسب روغن عملیات فلزکاری انتخاب و استفاده گردد.
تبخیر، پاشش و پخش شدن ذرات مه مانند روغن عملیات فلزکاری از مشکلات دیگری است که ممکن است مزاحمت ایجاد نماید که این مشکل میتواند ناشی از عواملی به شرح زیر باشد:
- افزایش بیش از حد دمای روغن که در این صورت با استفاده از یک سیستم سرد کننده مناسب، بصورت مستمر میتوان دمای روغن عملیات فلزکاری را کنترل نمود.
- بالا بودن میزان تبخیر روغن که این مورد با انتخاب یک روغن مناسب بر اساس دمای کاری در عملیات فلزکاری میتواند کنترل گردد.
- بالا بودن میزان تشکیل ذرات مه مانند روغن که با اضافه نمودن مواد افزودنی مناسب میتوان وجود این ذرات مه مانند را کنترل نمود.
- مشکل بروز علائم حساسیت های پوستی و ریوی بر پوست و ریه کارکنان در تماس با روغنهای فلزکاری که جهت مقابله با این مشکل توصیه میگردد ار روغنهای با شدت آسیب رسانی کمتر استفاده گردد و اطمینان حاصل نمود که کارکنان در معرض تماس با این روغنها از تجهیزات محافظت فردی مناسب استفاده نمایند.
- مشکل تغییر رنگ و کدورت روغن عملیات فلزکاری که با افزایش تعداد فیلترها و استفاده از مکانیزم های فیلتراسیون پیشرفته تر میتوان با سرعت و راندمان بالاتری آلودگی ها را از روغن عملیات فلزکاری خارج نمود و از کدورت ناشی از حضور ذرات آلوده کننده در درون روغن کاست همچنین با جایگزین نمودن بخشی یا تمامی روغن کار کرده با روغن نو، میتوان نسبت به اصلاح رنگ روغن اقدام نمود.
- مشکل بو گرفتن روغن عملیات فلزکاری که این مشکل میتواند با انتخاب روغن مناسبتر و مقاوم تر در مقابل دمای بالا و رشد باکتری ها و همچنین با اضاقه نمودن مواد افزودنی ضد باکتری به اندازه لازم، بر طرف گردد.
در مورد آن دسته از روغنهای عملیات فلزکاری که بصورت امولسیون شیری رنگ محلول در آب استفاده میگردند، مشکلات حادث شده بیشتر بوده که برخی از مهمترین موارد مربوطه و راه حل های پیشنهادی به شرح زیر میباشند:
تشکیل کف: در صورتیکه، در حین کار با این دسته از روغنهای عملیات فلزکاری، کف مشاهده گردد، این کف میتواند ناشی از مواردی به شرح زیر باشد:
- در صورت استفاده از آب نرم برای ساخت امولسیون روغن در آب، تشکیل کف در اولسیون مذکور تشدید میگردد و لذا لازم است سختی آب مورد استفاده، تحت کنترل باشد تا آب بیش از حد اصطلاحا نرم نباشد.
- ورود روغن های صنعتی سرگردان دیگر یا گریس ها به روغن در حال کار که در این حالت لازم است در اسرع وقت و با مشاهده کف، محل نشت روغن های سرگردان یا گریسهای نشت پیدا کرده، پیدا شده و از ورود آنها جلوگیری بعمل آورده شود و مواد افزودنی ضد کف به اندازه لازم، به محفظه روغن اضافه نمود.
- ورود جریانی از هوا به امولسیون روغن که این هوا میتواند باعث تشکیل کف زیادی در امولسیون روغن گردد و لازم است در اسرع وقت محل ورود جریان هوا شناسایی شده و از ورود آن به روغن در کار جلوگیری بعمل آورده شود.
- شروع واکنشهای میکرو بیولوژیکی که منجر به رشد میکروارگانیزم ها در امولسیون روغن میگردد و برای مقابله با این پدیده میتوان جریان سیرکولاسیون امولسیون روغن را تنظیم مجدد نمود، غلظت و pH امولسیون روغن را در حد مناسب کنترل نموده و در صورت لزوم بخشی یا تمامی امولسیون روغن را با اولسیون تازه تعویض کرد.
- در صورتیکه مقدار مواد افزودنی ضد کف درون روغن کم شده باشد با اضافه نمودن این مواد به اندازه کافی میتوان تشکیل کف را تحت کنترل در آورد.
- در صورتیکه غلظت امولسیون روغن بیش از حد زیاد شده باشد، میتوان با اضافه نمودن نیم درصد از امولسیون روغن تازه به محفظه روغن نسبت به کاهش غلظت اقدام نموده و تا رسیدن به غلظت مطلوب چند بار این کار را تکرار کرد.
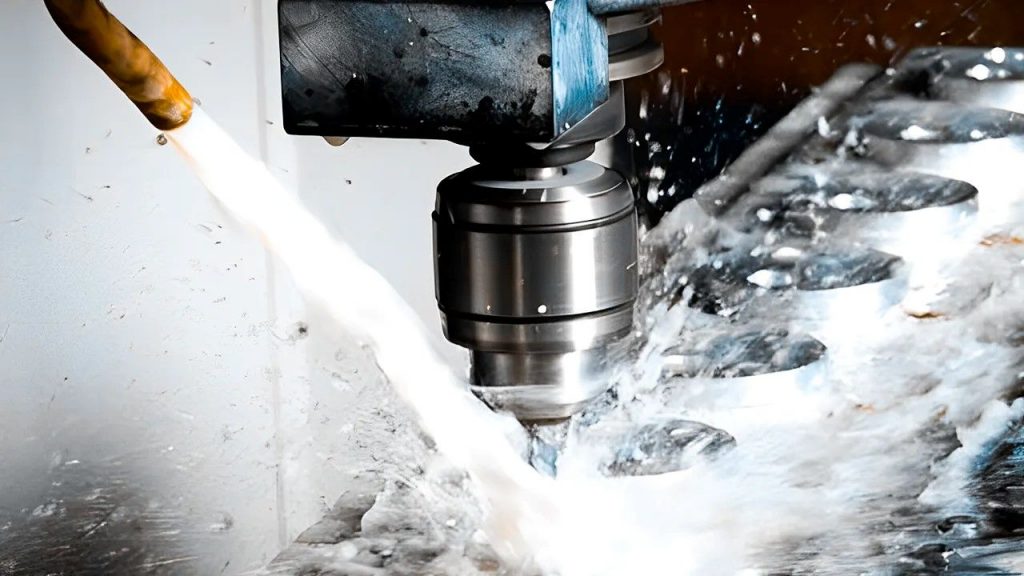
قابلیت های روغن مخصوص عملیات فلز کاری
مشکل بو گرفتن امولسیون روغن عملیات فلزکاری از مشکلات بسیار رایج این نوع از روغن هاست که این مشکل میتواند ناشی از مواردی به شرح زیر باشد:
- افزایش میزان مواد آلوده کننده در امولسیون روغن که در این صورت باید پروسه فیلتراسیون و تمیزکاری امولسیون روغن را به تعداد بیشتر و در زمانهای کوتاهتر انجام داد.
- طولانی شدن زمان توقف خطوط تولید که در این حالت با افزایش زمان سیرکولاسیون و افزایش تهویه هوای روی سطح امولسیون روغن میتوان طبعات ناشی از توقف خط تولید را کاهش داد.
- در صورت کاهش شدید pH امولسیون روغن، لازم است با مواد افزودنی مناسب pH امولسیون روغن کنترل شده و به حد مطلوب برگردانده شود.
ناپایداری امولسیون روغن میتواند منجر به شکسته شدن امولسیون و جدا شدن آب و روغن گردد که برای جلوگیری از این پدیده مواردی به شرح زیر توصیه میگردد:
- در زمان ساخت امولسیون روغن و آب، شدت به هم زدن در تشکیل امولسیون پایدار آب و روغن نقش بسیار مهمی را دارا است و لذا لازم است آب و روغن با شدت لازم به هم زده شوند تا امولسیونی پایدار تشکیل گردد.
- در صورت کاهش شدید pH امولسیون روغن، ناپایداری امولسیون روی خواهد دارد و لذا لازم است با افزودن، مواد افزودنی مناسب pH کنترل شده و به حد مطلوب برگردانده شود.
- افزایش سختی آب از موارد دیگری است که میتواند منجر به ناپایداری امولسیون روغن گردد و در این حالت لازم است با اضافه نموده امولسیون تازه، سختی امولسیون را به حد مطلوب برگرداند.
- افزایش میزان مواد آلوده کننده نیز میتواند باعث ناپایداری امولسیون روغن گردد و به همین دلیل لازم است که تا حد ممکن از ورود مواد آلوده کننده جلوگیری بعمل آورده شود و در صورت افزایش مقدار مواد آلوده کننده، لازم است پروسه فیلتراسیون و تمیزکاری امولسیون روغن را تقویت نمود.
- میزان خورندگی امولسیون روغن از پارامترهای مهم دیگری است که لازم است تحت کنترل قرار داشتته باشد و این کنترل با انجام مواردی به شرح زیر میتواند انجام گردد:
- در صورت کاهش pH امولسیون روغن از سطح مطلوب، میزان خوردندگی این امولسیون افزایش میابد و لذا لازم است با افزودن، مواد افزودنی مناسب pH کنترل شده و به حد مطلوب برگردانده شود.
- افزایش میزان کلراید آب از موارد دیگری است که میتواند منجر به افزایش شدت خورندگی امولسیون گردد و در این حالت لازم است با چایگزین نمودن مقداری از امولسیون با امولسیون تازه میزان کلراید در امولسیون را به حد مطلوب برگرداند.
- افزایش میزان کنداکتیویتی یا هدایت الکتریکی امولسیون، یکی دیگر از نشانه های افزایش میزان خورندگی امولسیون روغن است و در این حالت لازم است با جایگزین نمودن مقداری از امولسیون با امولسیون تازه میزان کنداکتیویتی در امولسیون را به حد مطلوب برگرداند.
مشکل بروز علائم حساسیت های پوستی و ریوی بر پوست و ریه کارکنان در تماس با امولسیون روغنهای فلزکاری از موارد مهم دیگری است که ممکن است مسئله ساز باشد و در ادامه به برخی از این موارد پرداخته شده است:
- هر دو حالت، بالا بودن یا پایین بودن غلظت و همچنین pH امولسیون میتواند برای پوست و ریه کارکنان در تماس با امولسیون روغن زیانبار باشد و لذا لازم است با افزودن مقادیری از امولسیون تازه و یا مواد مناسب نسبت به کنترل غلظت و pH امولسیون اقدام گردد.
- در صورتیکه تعداد میکرو ارگانیزم ها و باکتریها در امولسیون روغن بیش از حد گردد، تماس کارکنان با این امولسیون میتواند برای سلامتی کارکنان مضر باشد و در این حالت باید عملکرد مواد ضد باکتری موجود در امولسیون بررسی شده و در صورت لزوم از مواد قویتر استفاده شود و سیستم تهویه در محوطه مربوطه تقویت شده و همچنین لازم است استفاده از تجهیزات حفاظت فردی در برابر میکروارگانیزم ها جدی گرفته شود.
مشکل تشکیل رسوب بر روی جداره درونی تجهیزات عملیات فلزکاری، یکی از مشکلات رایج کار با امولسیون روغن میباشد و این مشکل میتواند از مواردی به شرح زیر ناشی گردد:
- غلظت زیاد امولسیون روغن میتواند منجر به تشکیل زود هنگام رسوب گردد که با اضافه کردن امولسیون تازه میتوان غلظت امولسیون را کنترل نمود.
- در صورتیکه زمان تمیزکاری جداره های داخلی تجهیزات عملیات فلزکاری، طولانی گردد و یا دمای امولسیون روغن بالاتر از حد مطلوب باشد این موضوع میتواند منجر به افزایش ضخامت لایه های رسوب شده و افزایش ضخامت رسوب منجر به افزایش خورندگی و گرفتگی خطوط لوله خواهد شد و لذا لازم است دمای کاری امولسیون روغن و زمان تمیزکاری تجهیزات با دقت مدیریت گردد.
- نوع مواد تمیز کننده نیز میتواند در تشکیل رسوبات تاثیر گذار باشد و چنانچه مشکل رسوب حاد گردد لازم است، مواد تمیزکتنده مناسبتری به خدمت گرفته شود.
- مشکلات ناشی از عدم فیلتراسیون مناسب امولسیون روغن نیز میتواند در نگهداری از این امولسیون بسیار تاثیر گذار باشد، در صورتیکه سختی آب، ورود روغنهای سرگردان، میزان رشد میکرو ارگانیزمها و تشکیل رسوبات کنترل نشود این موارد میتوانند باعث گرفتگی زود هنگام فیلترها شوند و لذا لازم است علاوه بر کنترل موارد فوق الذکر نسبت به اضافه نمودن مواد پاک کننده مناسب و تقویت سیستم فیبتراسیون اقدام نمود.
سخن پایانی
به عنوان یک توصیه کلی، میتوان گفت، در زمان استفاده از هر یک از دو نوع روغن عملیات فلزکاری (چه بصورت خالص و چه بصورت امولسیون شیری رنگ محلول در آب) انجام اقدامات پیشگیرانه و توجه بیشتر به آموزش نکات مریوط به نگهداری درست از روغن عملیات فلزکاری در حال کار، میتواند یک راهکار بسیار موثر باشد. جهت دریافت خدمات مشاوره فنی و تخصصی در زمینه انتخاب روغن های عملیات فلزکاری مناسب و افزایش اطلاعات کارکنان خطوط تولید در زمبنه نگهداری از روغن های عملیات فلزکاری در حال کار، میتوانید با دفتر شرکت بازرگانی رجال تماس حاصل نمایید.